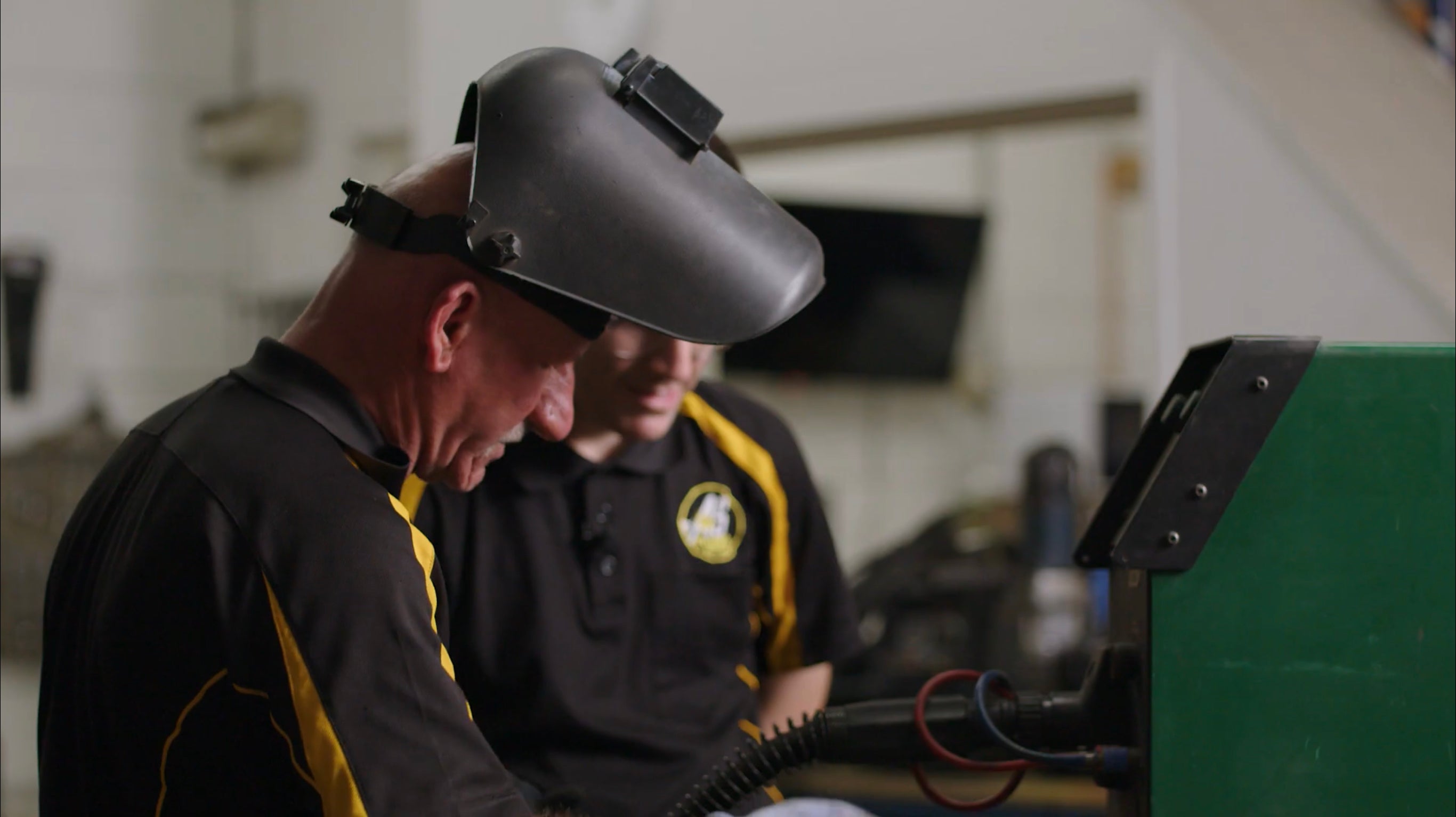
Servicing & Repairs
Expert maintenance and fast repairs for welding and electrical equipment
How to Book a Repair
-
1. Contact Us
Reach us by:
Phone: (02) 9729 1127
Email: office@aandswelding.com.au
We’ll confirm your needs and explain the next steps. -
2. Bring In Your Equipment
Choose the option that suits you best:
Self Drop-off & Pick-up (fastest, no added cost)
Courier Drop-off & Pick-up (light equipment only)
Freight Shipping (light & heavy equipment, Australia-wide and international coverage)
-
3. Assessment & Quote
Our specialists inspect your equipment and provide a detailed breakdown:
Repair Assessment: Clear costs for restoring your equipment
Servicing Needs: Recommendations for additional fixes or adjustments -
4. Repair & Collection
We complete the work quickly and reliably, then return your equipment via:
Self Pick-up (during business hours)
Courier or Freight Shipping (with the transport option arranged at booking)
Our simple step-by-step process
Inside Our Workshop
1. Disassembly & Cleaning
We carefully disassemble your equipment and remove dust and debris from internal components, ensuring a clean inspection.
2. Investigation & Assessment
Using our custom bench-testing units, we evaluate outputs and identify any faults such as blown diodes, missing components, or irregular voltage/amperage.
3. Fault Repair & Testing
We replace or repair faulty components using in-stock parts (or order specialised components if required). Once complete, we conduct a thorough weld test across different modes, gas types, and environments.
4. Labelling & Documentation
After reassembly and a final clean, we provide full documentation — including invoices, warranties, and maintenance records — to ensure compliance with SafeWork standards.
Brands We Service & Support
-
IRONWELD
-
BOSSWELD
-
UNIMIG
-
Lincoln Electric
-
Kemppi
-
JASIC
-
ESAB
-
CIGWELD
-
WIA
-
Miller
-
Weldclass
-
Nitto Kohki
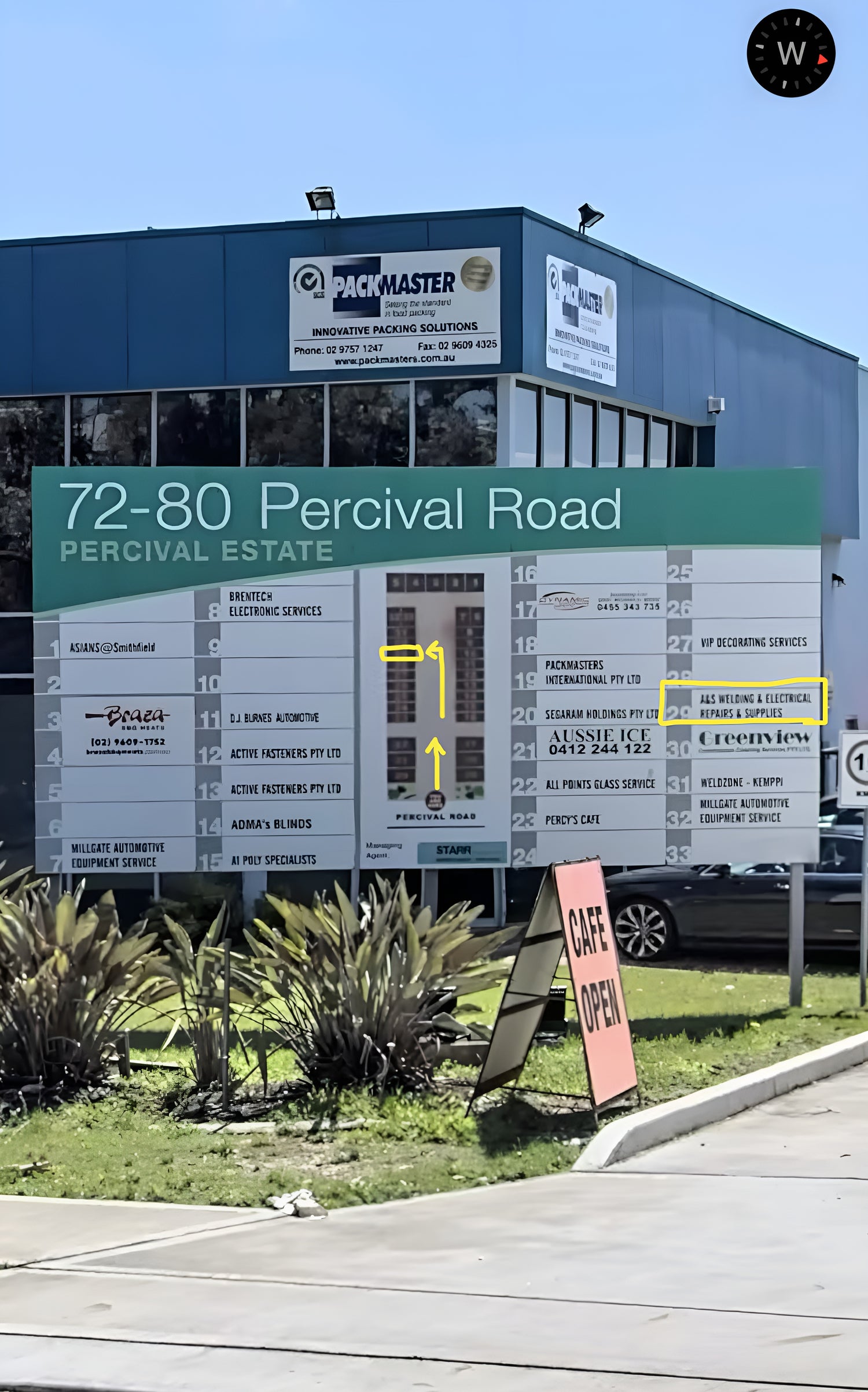
Organise a Service / Repair
Bring your equipment to A&S for fast, reliable, and affordable repairs. Our skilled team will get your gear back to work quickly and with the care you expect.
For assistance, contact us during business hours on (02) 9729 1127, or reach out by email, live chat, or the contact form below.
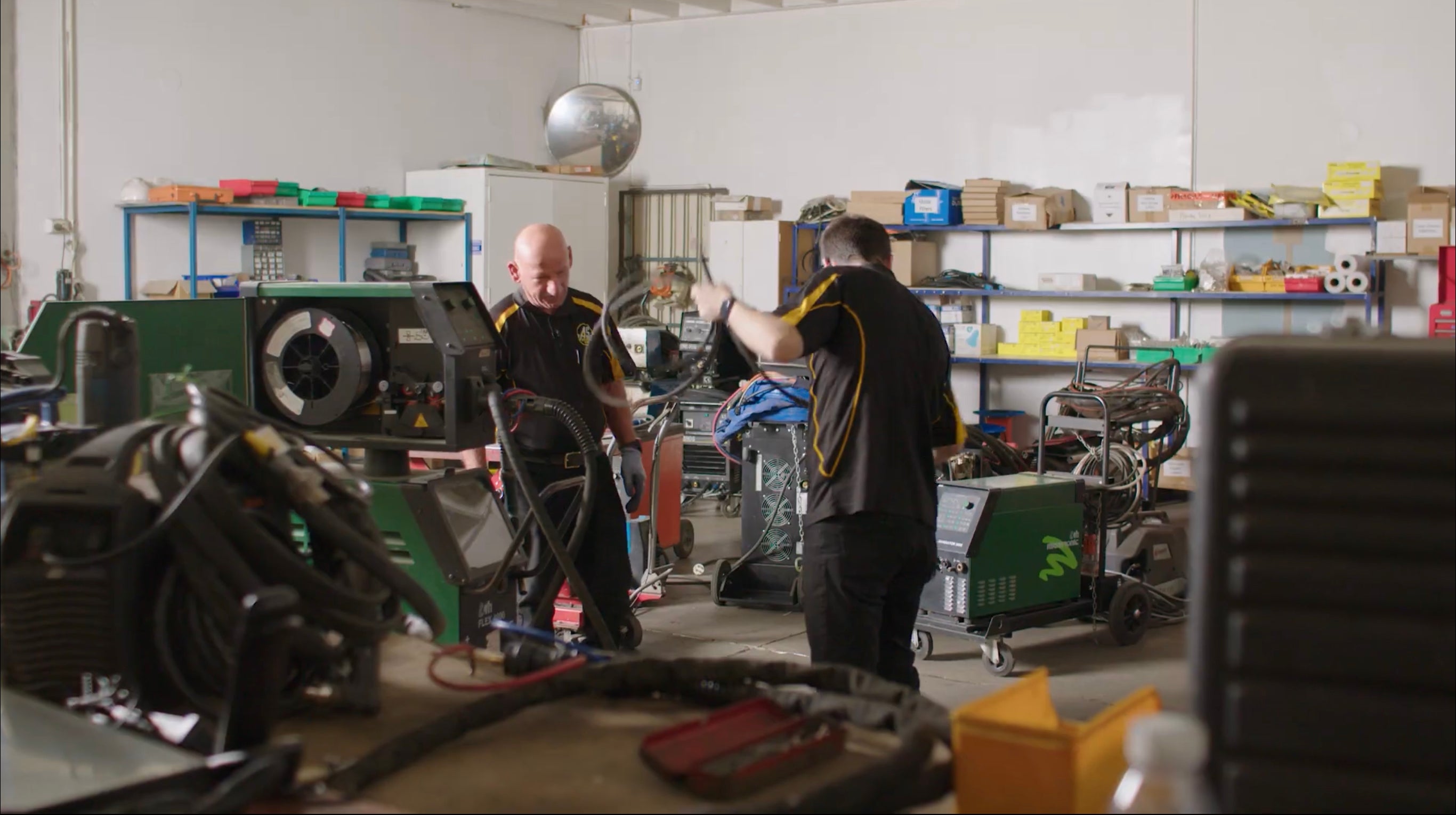

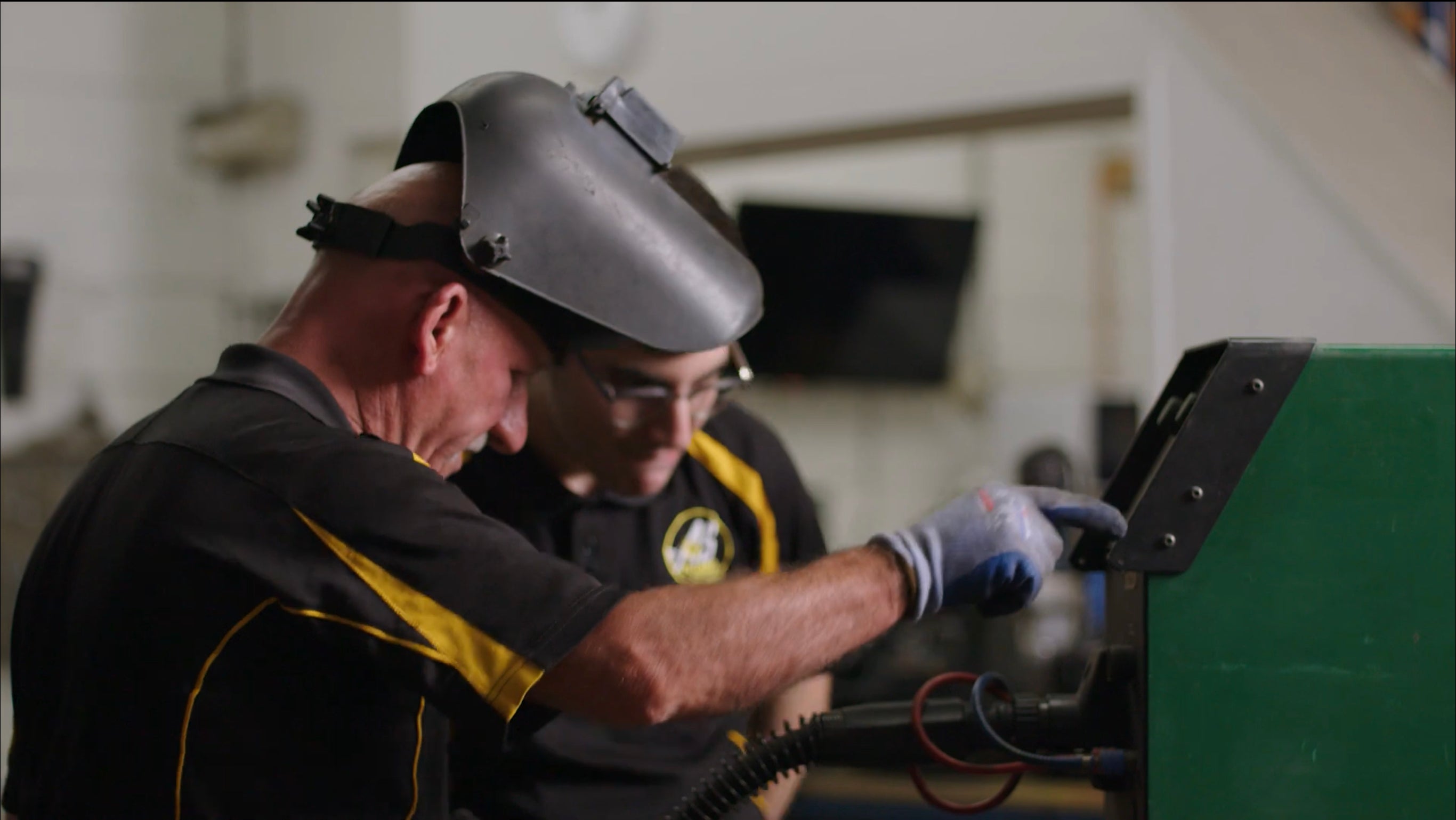
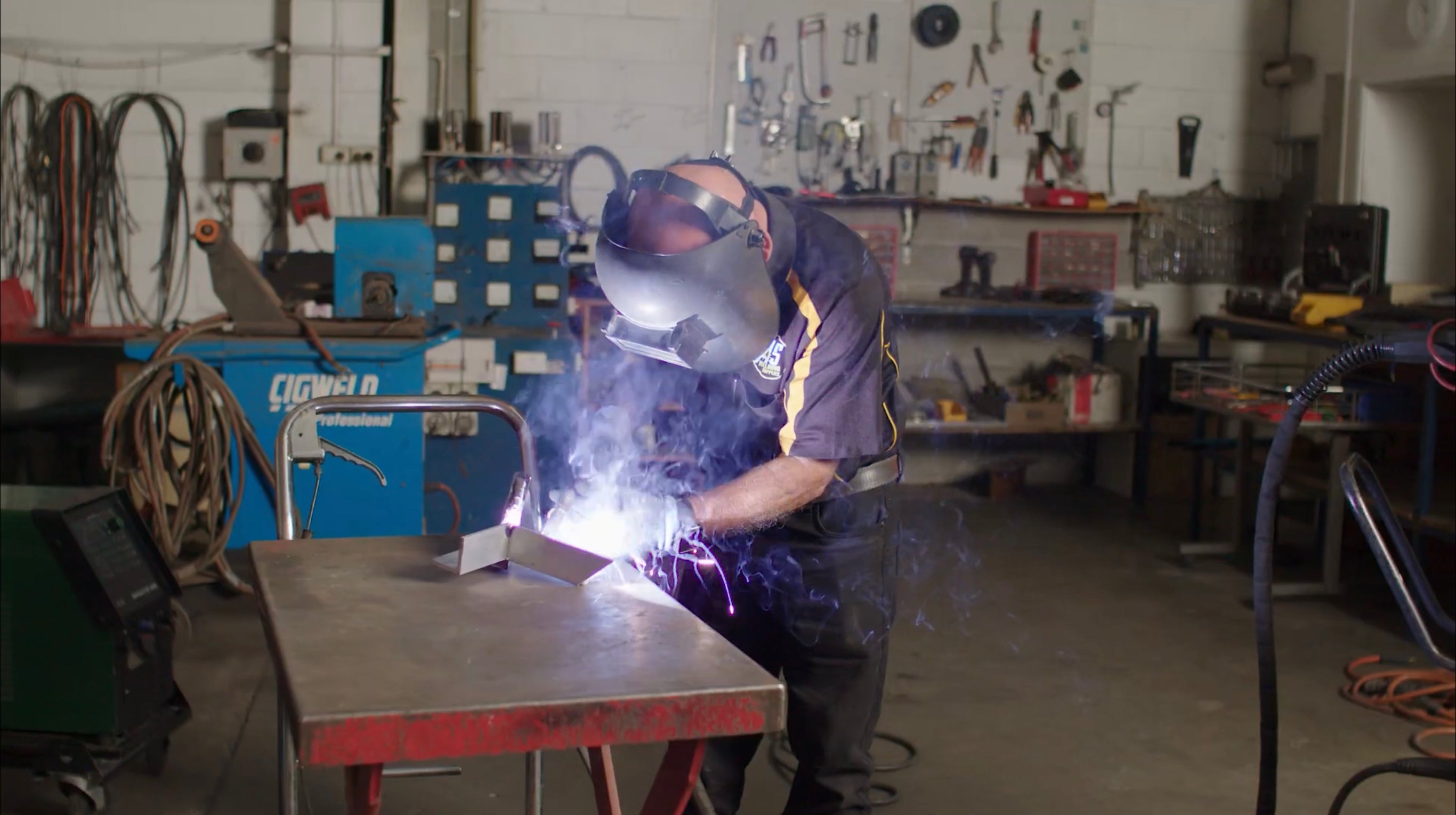
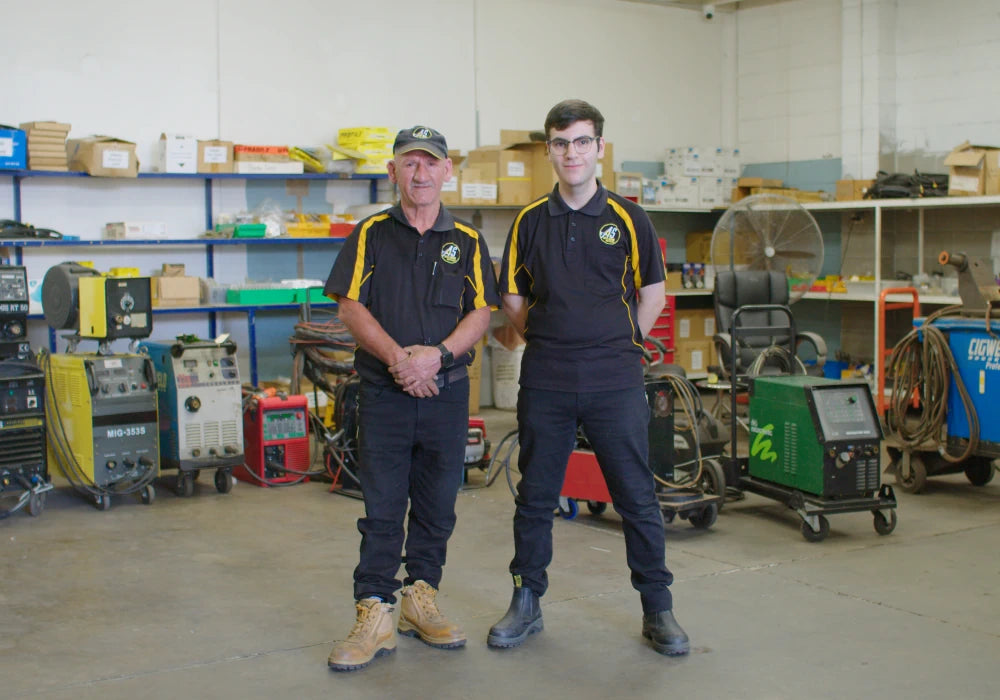